اردیبهشت 1, 1404
آیا تا به حال هنگام جوشکاری، با این سوال مواجه شدهاید که کدام الکترود انتخاب بهتری است؟
در ظاهر شاید تفاوت بین انواع الکترودها کمرنگ به نظر برسد، اما در واقع انتخاب نادرست میتواند کیفیت جوش را بهطور جدی تحتتأثیر قرار دهد؛ از ترکهای سطحی گرفته تا عدم استحکام سازه. به همین دلیل، شناخت ویژگیهای فنی و کاربردی هر نوع الکترود، برای هر جوشکاری—چه حرفهای باشید، چه تازهکار—ضروری است.
در میان دهها نوع الکترود موجود در بازار، دو مدل E6013 و E7018 از محبوبترین و پرکاربردترین گزینهها هستند. الکترود 6013 به دلیل کاربری آسان و جوشکاری نرم و تمیز، انتخاب اول بسیاری از کاربران خانگی و پروژههای سبک است. در مقابل، 7018 به مقاومت بالا، نفوذ عمیق و جوشکاری مطمئن در سازههای سنگین و حساس معروف است.
اما سؤال اصلی اینجاست: کدامیک برای کار شما مناسبتر است؟ در این مقاله، با مقایسهای جامع بین این دو الکترود، تمام تفاوتها، مزایا، معایب و کاربردهایشان را بررسی میکنیم تا بتوانید بهترین انتخاب را برای پروژه بعدیتان داشته باشید.
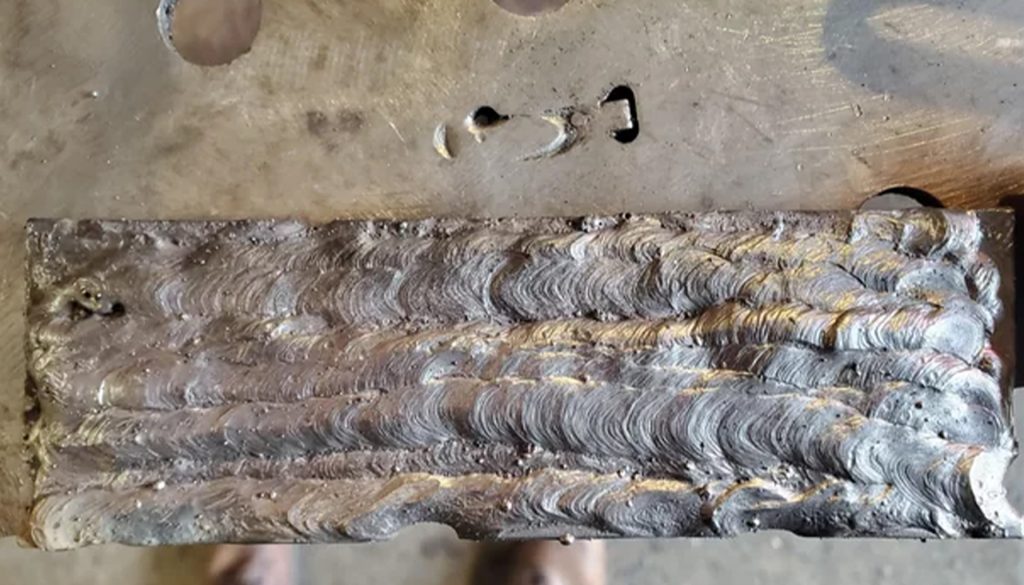
مشخصات الکترود 6013
الکترود E6013 به حق یکی از پرکاربردترین و شناختهشدهترین انواع الکترودهای پوششدار در فرآیند جوشکاری دستی قوسی (SMAW – Shielded Metal Arc Welding) در سراسر جهان است. این الکترود، به دلیل سهولت کاربری مثالزدنی و ارائهی کیفیت ظاهری مناسب در خط جوش، جایگاه ویژهای هم در محیطهای کارگاهی کوچک و پروژههای سبک صنعتی یافته است و هم به انتخاب اول بسیاری از علاقهمندان و کاربران خانگی برای تعمیرات و سازههای غیرحساس تبدیل شده است. در این بخش، قصد داریم نگاهی عمیقتر به مشخصات فنی، ساختار منحصربهفرد، نحوهی عملکرد و همچنین محدودیتهای کاربرد این الکترود محبوب داشته باشیم.
نوع روکش و تأثیر آن بر عملکرد (ترکیب شیمیایی روکش)
یکی از مهمترین ویژگیهای الکترود 6013، نوع پوشش آن است که عمدتاً از نوع روتیلی-سلولزی با سهم قابل توجهی دیاکسید تیتانیوم (TiO₂) تشکیل شده است. این ترکیب خاص در روکش الکترود، تأثیرات کلیدی بر فرآیند جوشکاری دارد:
- قوس نرم و پایدار: وجود دیاکسید تیتانیوم باعث یونیزاسیون آسانتر فضای اطراف قوس میشود. این پدیده منجر به روشن شدن بسیار سادهی قوس، حتی با دستگاههای جوش کوچک یا ضعیف، و همچنین پایداری عالی قوس در حین جوشکاری میشود که این خود، فرآیند را برای جوشکاران مبتدی بسیار راحت و قابل کنترل میکند.
- پاشش کم (Low Spatter): این نوع روکش باعث میشود مذاب حین جوشکاری به صورت کنترلشدهتری منتقل شود و در نتیجه، مقدار پاشش دانههای مذاب به اطراف ناحیهی جوش به حداقل برسد. این ویژگی به تمیز ماندن قطعه کار و کاهش نیاز به پاکسازی پس از جوش کمک میکند.
- شکلدهی عالی به گردهی جوش: سربارهای که از سوختن این روکش حاصل میشود، بسیار روان و قابل کنترل است و به زیبایی روی خط جوش قرار میگیرد. این سرباره به شکلدهی منظم و تمیز گردهی جوش کمک کرده و ظاهری زیبا و حرفهای به جوش نهایی میبخشد که نیاز به عملیات پرداختکاری سنگین را کاهش میدهد.
سازگاری با انواع جریان جوشکاری (نوع جریان و پلاریته)
الکترود E6013 انعطافپذیری بالایی از نظر نوع جریان مصرفی دارد. این الکترود هم با جریان مستقیم (DC) در هر دو پلاریته مثبت (DC+) و منفی (DC-) و هم با جریان متناوب (AC) قابل استفاده است.
- اوج کارایی با جریان AC: با این حال، عملکرد بهینه و روانترین قوس را الکترود 6013 هنگام استفاده از جریان AC به نمایش میگذارد. این سازگاری عالی با جریان AC یک مزیت بزرگ محسوب میشود، زیرا دستگاههای جوش ترانسفورماتوری ساده و ارزانقیمت خانگی معمولاً فقط خروجی AC دارند و 6013 امکان استفادهی موثر از این دستگاهها را فراهم میکند.
- کاربرد با DC: هرچند با جریان DC نیز میتوان جوشکاری کرد، اما قوس ممکن است کمی متفاوت باشد و مزیت اصلی 6013 که همان سهولت کاربری و قوس نرم است، با AC بیشتر نمایان میشود.
انعطافپذیری در موقعیتهای جوشکاری (وضعیتهای مجاز جوشکاری)
یکی دیگر از نقاط قوت 6013، قابلیت جوشکاری آن در تمام وضعیتهای استاندارد جوشکاری است: وضعیت تخت (Flat – 1F/1G)، افقی (Horizontal – 2F/2G)، عمودی (Vertical – 3F/3G)، و سقفی (Overhead – 4F/4G).
- عملکرد بهینه در وضعیتهای تخت و افقی: به دلیل سیالیت مناسب مذاب و سرباره، بهترین و آسانترین جوشکاری با این الکترود در وضعیتهایی انجام میشود که نیروی جاذبه به نشستن صحیح مذاب و سرباره کمک میکند، یعنی در موقعیتهای تخت و افقی.
- قابلیت جوشکاری در وضعیتهای عمودی و سقفی: جوشکاری در وضعیتهای عمودی (صعودی یا نزولی) و به خصوص سقفی، نیاز به مهارت و کنترل بیشتری از سوی جوشکار دارد. جوشکار باید بتواند با تکنیکهای خاصی، از ریزش مذاب و سرباره به دلیل نیروی جاذبه جلوگیری کرده و شکل مناسب گردهی جوش را حفظ کند. پس هرچند 6013 قابلیت این وضعیتها را دارد، اما برای دستیابی به جوش باکیفیت در آنها، تجربه و دقت بیشتری لازم است.
مزایای کلیدی 6013 : چرا 6013 انقدر محبوب است؟
مجموعهی ویژگیهای الکترود 6013 منجر به مزایای مهمی شده که آن را برای طیف وسیعی از کاربردها مناسب میسازد:
- شروع قوس بسیار آسان و پایداری بالا: این ویژگی، آن را به گزینهای ایدهآل برای افراد تازهکار تبدیل کرده و در هر بار شروع جوشکاری، فرآیند را تسهیل میبخشد.
- مناسب برای جوشکاری ورقها و مقاطع نازک: به دلیل نفوذ نسبتاً کنترلشده و قوس نرم، خطر سوراخ شدن یا سوختن ورقهای فلزی نازک در حین جوشکاری با این الکترود کمتر است.
- ظاهر خط جوش بسیار تمیز و نیاز کم به پاکسازی پس از جوش: سربارهی حاصل از روکش به راحتی جدا میشود و گردهی جوش معمولاً سطحی صاف و منظم دارد که زمان و هزینهی پرداختکاری را کاهش میدهد.
- سازگاری عالی با هر دو نوع جریان AC و DC: این امکان استفاده از انواع دستگاههای جوش، از جمله دستگاههای ترانسفورماتوری ساده، را فراهم میآورد.
- در دسترس بودن و قیمت مناسب: الکترود 6013 به طور گسترده در بازار یافت میشود و نسبت به بسیاری از الکترودهای تخصصیتر، قیمت پایینتری دارد.
محدودیتها: شناخت نقاط ضعف برای کاربرد صحیح
با وجود تمام مزایا، الکترود 6013 محدودیتهایی نیز دارد که شناخت آنها برای انتخاب صحیح الکترود در کاربردهای مختلف ضروری است:
- عمق نفوذ کمتر: روکش حاوی مقدار زیاد سرباره باعث میشود انرژی قوس بیشتر صرف ذوب کردن روکش و الکترود شود و نفوذ در فلز پایه نسبت به الکترودهایی مانند E7018 که پوشش متفاوتی دارند و قوس متمرکزتری ایجاد میکنند، کمتر باشد. این نفوذ کم برای سازههایی که نیاز به اتصال قوی در عمق دارند، محدودیت ایجاد میکند.
- مقاومت پایینتر در برابر ترکخوردگی: فلز جوش حاصل از 6013 معمولاً چقرمگی (Toughness) و مقاومت کمتری در برابر تشکیل ترک، به خصوص در فولادهای پرکربنتر یا در معرض تنشهای بالا یا دماهای پایین، دارد.
- نامناسب برای سازههای تحت فشار، بارهای دینامیکی یا سازههای بحرانی: به دلیل مقاومت کششی (Tensile Strength) و چقرمگی نسبتاً پایینتر فلز جوش، این الکترود برای جوشکاری لولهها یا مخازن تحت فشار، قطعات ماشینآلات سنگین که در معرض لرزش و بارهای متغیر هستند، یا سازههایی که failure در آنها عواقب جدی دارد (مانند پلها، ساختمانهای بلند) توصیه نمیشود. الکترودهای با خواص مکانیکی بالاتر (مثل E7018) برای این کاربردها مناسبترند.
مشخصات الکترود 7018 و عملکرد آن
الکترود E7018 یکی از مهمترین و پرکاربردترین الکترودها در جوشکاری دستی قوسی (SMAW)، به خصوص در کاربردهای سنگین صنعتی و سازههای بحرانی است. برخلاف الکترودهای همهکاره مانند 6013، الکترود 7018 به دلیل خواص مکانیکی فوقالعادهی فلز جوش و پوشش قلیایی کمهیدروژن خود شناخته میشود و برای جوشکاری فولادهایی که نیاز به استحکام بالا، چقرمگی خوب و مقاومت در برابر ترک دارند، گزینهی اول متخصصان جوش است.
ساختار، پوشش قلیایی (Low Hydrogen)، و پایداری قوس
- ساختار و پوشش قلیایی (کمهیدروژن): الکترود 7018 دارای یک مفتول فولادی در هسته است، اما ویژگی اصلی آن در پوشش ضخیم و قلیایی آن نهفته است. این پوشش عمدتاً از مواد قلیایی مانند کربنات کلسیم (CaCO₃) و فلورید کلسیم (CaF₂) تشکیل شده است. مهمترین نقش این پوشش، تولید گاز محافظ با حداقل میزان هیدروژن در حین سوختن در دمای قوس است. میزان هیدروژن در فلز جوش حاصل از این الکترود بسیار پایین نگه داشته میشود، به همین دلیل به آنها الکترودهای “کمهیدروژن” (Low Hydrogen) گفته میشود. این ویژگی حیاتیترین عامل در پیشگیری از پدیدهی “هیدروژن تردی” (Hydrogen Embrittlement) یا ترکهای سرد در ناحیهی جوش و مناطق اطراف آن (HAZ) است که در جوشکاری فولادهای با استحکام بالا یا مقاطع ضخیم، یک مشکل جدی و عامل شکست محسوب میشود.
- پایداری قوس: الکترود 7018 قوسی نرم، پایدار و متمرکز ایجاد میکند. شروع قوس با این الکترود ممکن است نسبت به 6013 کمی نیاز به مهارت بیشتری داشته باشد، اما پس از برقراری، قوس بسیار یکنواخت میسوزد. این الکترود سربارهی سنگین و متراکمی تولید میکند که به خوبی حوضچهی مذاب را پوشانده و از تماس آن با اتمسفر و جذب آلودگیها محافظت میکند. این سرباره پس از سرد شدن معمولاً کمی سختتر از سربارهی 6013 جدا میشود.
خواص مکانیکی برجسته الکترود E7018 و کاربردهای سنگین صنعتی
الکترود E7018 برای جوشکاری فولادهای کربنی و کمآلیاژ با استحکام کششی حداقل 70,000 psi (حدود 480 مگاپاسکال) طراحی شده است (عدد 70 در نام E7018 نشاندهنده این استحکام است). فلز جوش حاصل از این الکترود دارای خواص مکانیکی بسیار خوبی است:
- استحکام کششی بالا: مناسب برای سازههایی که تحت بارهای زیاد قرار دارند.
- چقرمگی (Toughness) عالی: مقاومت بالایی در برابر شکست ترد، به خصوص در دماهای پایین، از خود نشان میدهد که برای سازههایی که در معرض ضربه یا دماهای زیر صفر هستند حیاتی است.
- قابلیت انعطاف (Ductility) مناسب: امکان تغییر شکل پلاستیک قبل از شکست را فراهم میکند.
این خواص برجسته، الکترود 7018 را به انتخابی ایدهآل برای طیف گستردهای از کاربردهای سنگین صنعتی و سازههای بحرانی تبدیل کرده است، از جمله:
- ساخت سازههای فلزی سنگین: مانند پلها، ساختمانهای بلندمرتبه، اسکلهها و سازههای فراساحلی.
- صنایع نفت، گاز و پتروشیمی: برای جوشکاری خطوط لوله (Pipelines)، مخازن تحت فشار (Pressure Vessels) و تجهیزات فرآیندی که نیاز به استحکام و ایمنی بسیار بالا دارند.
- ماشینآلات سنگین: جوشکاری قطعات لودرها، بلدوزرها، جرثقیلها و سایر تجهیزات معدنی و عمرانی.
- صنایع دریایی: ساخت و تعمیر کشتیها و سکوهای نفتی.
- ساخت و تعمیر دیگهای بخار و مخازن تحت دماهای متغیر.
نیاز حیاتی به خشککردن و نگهداری در شرایط خاص (حساسیت به رطوبت)
یکی از مهمترین نکات در استفاده از الکترود 7018 که آن را از الکترودهایی مانند 6013 متمایز میکند، حساسیت شدید پوشش آن به رطوبت و لزوم نگهداری و خشککاری در شرایط خاص است.
- چرا رطوبت مشکلساز است؟ همانطور که گفته شد، هدف اصلی پوشش قلیایی، کم کردن میزان هیدروژن در جوش است تا از ترکخوردگی جلوگیری شود. اما این پوشش قلیایی به شدت جاذب رطوبت محیط (Hygroscopic) است. اگر الکترود رطوبت جذب کند، هنگام جوشکاری، این رطوبت در دمای بسیار بالای قوس به هیدروژن تجزیه میشود. هیدروژن آزاد شده وارد فلز جوش مذاب میشود و هنگام سرد شدن فلز، میتواند منجر به ایجاد ترکهای میکروسکوپی یا ماکروسکوپی شود که به آنها ترکهای سرد (Cold Cracks) یا ترکهای تأخیری (Delayed Cracks) گفته میشود. این ترکها حتی ممکن است ساعتها یا روزها پس از اتمام جوشکاری ظاهر شوند و استحکام و ایمنی اتصال را به شدت کاهش دهند.
- روشهای صحیح نگهداری: الکترودهای 7018 نو باید حتماً در بستهبندیهای اصلی، کاملاً پلمپ و ضد رطوبت (معمولاً قوطیهای فلزی یا بستههای وکیوم شده) نگهداری شوند. پس از باز کردن بسته، الکترودها باید فوراً به آونهای نگهداری (Holding Ovens) منتقل شوند و در دمای مشخصی (معمولاً حدود ۱۲۰ تا ۱۵۰ درجه سانتیگراد) نگهداری شوند تا از جذب مجدد رطوبت محیط جلوگیری شود. این دما صرفاً برای نگهداری و حفظ وضعیت کمهیدروژن الکترود است.
- خشککاری مجدد (Reconditioning/Baking): اگر الکترودها برای مدتی (بسته به رطوبت محیط، ممکن است تنها چند ساعت) در معرض هوای آزاد قرار بگیرند، رطوبت جذب میکنند و خواص کمهیدروژن بودن خود را از دست میدهند. در این حالت، قبل از استفاده، باید حتماً در آونهای خشککاری (Baking Ovens) و در دماهای به مراتب بالاتر (معمولاً بین ۲۵۰ تا ۴۵۰ درجه سانتیگراد، بسته به توصیهی سازنده) و برای مدت زمان مشخصی (معمولاً ۱ تا چند ساعت) خشککاری مجدد شوند. این فرآیند رطوبت جذب شده را خارج میکند. الکترودهایی که خشککاری مجدد شدهاند نیز پس از اتمام کار باید دوباره به آون نگهداری بازگردانده شوند. الکترودهایی که برای مدت طولانی در معرض رطوبت بودهاند و یا چند بار خشککاری مجدد شدهاند، ممکن است دیگر قابل استفاده در کاربردهای بحرانی نباشند.
مقایسه الکترود 6013 و 7018 از لحاظ عملکرد و کاربرد
در دنیای جوشکاری دستی قوسی (SMAW)، الکترودهای E6013 و E7018 دو نمونهی بسیار شناخته شده هستند، اما هر یک ویژگیها و کاربردهای متمایزی دارند. شناخت این تفاوتها برای انتخاب الکترود مناسب جهت دستیابی به جوش باکیفیت و ایمن ضروری است.
تفاوت در نوع پوشش و جوشدهی
یکی از اصلیترین تفاوتهای این دو الکترود در نوع پوشش فلاکس آنهاست که مستقیماً بر خواص جوشدهی تأثیر میگذارد:
- الکترود 6013: دارای پوشش عمدتاً روتیلی-سلولزی است. این پوشش باعث ایجاد قوس الکتریکی نرم و آرام میشود که شروع آن بسیار آسان است. پاشش (Spatter) حین جوشکاری با 6013 معمولاً کم است و سربارهای تولید میکند که به راحتی جدا میشود. دود حاصل از جوشکاری با این الکترود نیز نسبت به برخی انواع دیگر کمتر آزاردهنده است. ظاهر گردهی جوش در 6013 عموماً صاف و زیباست.
- الکترود 7018: دارای پوشش قلیایی (Basic) یا کمهیدروژن (Low-Hydrogen) است. این نوع پوشش باعث ایجاد قوسی پایدار و متمرکزتر میشود که نفوذ عمیقتری در فلز پایه ایجاد میکند. پاشش 7018 نیز کنترل شده است، اما سربارهی آن سنگینتر و متراکمتر از 6013 بوده و جدا کردن آن معمولاً کمی دشوارتر است. دود حاصل از 7018 ممکن است کمی بیشتر باشد. مهمترین مزیت این پوشش، به حداقل رساندن میزان هیدروژن در فلز جوش است.
تفاوت در مقاومت و استحکام نهایی جوش
کیفیت پوشش فلاکس و ترکیب شیمیایی آن تأثیر مستقیمی بر خواص مکانیکی و متالورژیکی فلز جوش نهایی دارد:
- الکترود 6013: فلز جوش حاصل از 6013 دارای مقاومت کششی (Tensile Strength) و چقرمگی (Toughness) کمتری نسبت به 7018 است. این الکترود برای جوشکاریهای عمومی و سازههای سبک یا غیرحساس مناسب است که تحت تنشها یا بارهای دینامیکی بالا قرار نمیگیرند. مقاومت آن در برابر ترکخوردگی نیز نسبت به 7018 پایینتر است.
- الکترود 7018: فلز جوش 7018 دارای خواص مکانیکی بسیار بالاتری است؛ استحکام کششی، استحکام تسلیم، چقرمگی و مقاومت به ضربه در این الکترود به مراتب بهتر است. به همین دلیل، 7018 برای جوشهای سازهای سنگین، سازههای تحت بار زیاد، قطعات بحرانی ماشینآلات و فولادهایی که مستعد ترکخوردگی هستند (به دلیل محتوای کربن بالاتر یا ضخامت زیاد) انتخاب استاندارد محسوب میشود. عدد 70 در نام آن نشاندهنده حداقل استحکام کششی (70 ksi) است.
بررسی سهولت استفاده و یادگیری
یکی از عواملی که باعث محبوبیت 6013 شده، سادگی کار با آن است، در حالی که 7018 نیاز به دقت بیشتری دارد:
- الکترود 6013: به دلیل شروع قوس بسیار آسان و قوس نرم و پایدار، استفاده از آن برای مبتدیها بسیار ساده است و به راحتی میتوان جوشکاری را با آن فرا گرفت. حساسیت کمتری نسبت به طول قوس و زاویهی الکترود دارد و به اصطلاح الکترود “همهکاره و خوشدست” است.
- الکترود 7018: شروع قوس با 7018 ممکن است کمی نیاز به تکنیک (ضربه زدن یا خراش دادن) داشته باشد. همچنین برای حفظ خواص کمهیدروژن آن، نیاز به شرایط نگهداری و خشککاری خاص دارد که استفاده از آن را در محیطهای کارگاهی غیرتخصصی یا مصارف خانگی با چالش روبرو میکند. به همین دلیل، 7018 بیشتر در پروژههای پیشرفته و حرفهای توسط جوشکاران با تجربه به کار میرود.
کاربردهای رایج برای هر الکترود
با توجه به تفاوتهای عملکردی و مکانیکی، کاربردهای اصلی این دو الکترود کاملاً از هم متمایز میشود:
- پروژههای خانگی و سبک برای 6013: الکترود 6013 انتخاب ایدهآل برای تعمیرات عمومی، ساخت نرده، فنس، قابهای فلزی سبک، و کارهای ورقکاری با ضخامت کم است. در هر جایی که نیاز به استحکام فوقالعاده بالا یا مقاومت در برابر ترک حیاتی نباشد و سهولت کار و ظاهر جوش اهمیت داشته باشد، 6013 گزینهی مناسبی است.
- کاربردهای سازهای و حساس مثل پلسازی برای 7018: الکترود 7018 در ساختمانسازی سنگین، پلسازی، خطوط لوله تحت فشار، کشتیسازی، ساخت ماشینآلات سنگین، و مخازن تحت فشار که ایمنی و استحکام جوش از اهمیت حیاتی برخوردارند، به کار میرود. در هر کاربردی که شکست جوش میتواند منجر به فاجعه شود یا در جوشکاری فولادهای پرمقاومت و ضخیم، 7018 الکترود استاندارد است.
- بحث در مورد جوش نفوذی و انتخاب الکترود مناسب: جوش نفوذی به توانایی الکترود در ذوب کردن و نفوذ به عمق فلز پایه در محل اتصال گفته میشود. الکترود 7018 به طور کلی نفوذ عمیقتر و قابل اطمینانتری نسبت به 6013 ارائه میدهد. این به دلیل ویژگیهای قوس و سربارهی آن است که امکان هدایت بهتر حرارت به ریشه اتصال را فراهم میآورد. بنابراین، برای جوشهای نفوذی که نیاز به اتصال کامل و قوی در تمام ضخامت قطعه دارند (مانند جوش شیاری در صفحات ضخیم)، 7018 الکترود بسیار مناسبتری است. در مقابل، 6013 نفوذ کمتری دارد و بیشتر برای جوشهای گوشه (Fillet Welds) یا جوش لب به لب بر روی ورقهای نازک که نفوذ عمیق ممکن است مشکلساز باشد، کاربرد دارد.
در نهایت، انتخاب بین 6013 و 7018 نه تنها به مهارت جوشکار، بلکه مهمتر از آن، به نوع کاربرد، جنس و ضخامت قطعه کار و الزامات استحکامی و ایمنی پروژه بستگی دارد.
کدام الکترود برای پروژه شما بهتر است؟
انتخاب الکترود مناسب، گام مهمی برای انجام یک جوشکاری موفق و ایمن است. بین الکترودهای 6013 و 7018، هیچ کدام ذاتاً “بهتر” از دیگری نیستند؛ بلکه هر یک برای کاربردهای خاصی بهینهسازی شدهاند. انتخاب شما باید بر اساس نیازهای مشخص پروژهتان و شناخت دقیق الکترودهای جوشکاری صورت گیرد.
انتخاب بر اساس نوع فلز پایه، ضخامت و موقعیت جوشکاری
برای انتخاب درست بین 6013 و 7018، لازم است عوامل مختلفی را در نظر بگیرید:
- نوع فلز پایه: الکترود 6013 عمدتاً برای جوشکاری فولادهای کربنی ساده و با کشش پایین مناسب است. در مقابل، 7018 برای جوشکاری فولادهای کربنی با استحکام بالاتر، فولادهای کمآلیاژ، و فولادهایی که مستعد ترکخوردگی هستند، گزینهی برتر است.
- ضخامت قطعه کار: 6013 به دلیل نفوذ کمتر، برای جوشکاری ورقهای نازک (مثلاً زیر 5 میلیمتر) مناسبتر است و خطر سوختن ورق را کاهش میدهد. 7018 با نفوذ عمیقتر خود، برای جوشکاری صفحات و مقاطع ضخیمتر که نیاز به استحکام و نفوذ کامل در ریشه اتصال دارند، ایدهآل است.
- موقعیت جوشکاری: هرچند هر دو الکترود قابلیت جوشکاری در تمام وضعیتها (تخت، افقی، عمودی، سقفی) را دارند، اما 6013 در وضعیتهای تخت و افقی بسیار آسان و در وضعیتهای عمودی و سقفی با کمی تمرین قابل استفاده است. 7018 نیز در تمام وضعیتها عالی عمل میکند، اما کنترل سربارهی سنگین آن در وضعیتهای عمودی و سقفی نیازمند مهارت بیشتری است.
جمعبندی
در مجموع، تفاوت اصلی بین الکترود 6013 و 7018 در این است که 6013 بر سهولت استفاده و ظاهر جوش در کارهای سبک تمرکز دارد، در حالی که 7018 بر استحکام، چقرمگی و مقاومت در برابر ترک در کاربردهای سنگین و بحرانی متمرکز است و این تفاوتها ناشی از نوع پوشش و متعاقباً خواص فلز جوش آنهاست. شرایط نگهداری نیز یک تمایز کلیدی است.
سوالات متداول درباره الکترودهای 6013 و 7018
کدام الکترود برای شروع یادگیری بهتر است؟
الکترود 6013 به دلیل شروع قوس بسیار آسان، قوس نرم و قابل کنترل و حساسیت کمتر نسبت به تکنیک جوشکار، بهترین گزینه برای شروع یادگیری جوشکاری دستی قوسی است.
آیا الکترود 7018 همیشه انتخاب بهتری است؟
خیر، 7018 همیشه انتخاب بهتری نیست. “بهترین” به نیازهای پروژه بستگی دارد. 7018 برای کاربردهای سازهای سنگین و بحرانی بهتر است، اما برای کارهای سبک، ورقهای نازک، یا مواقعی که سهولت استفاده و عدم نیاز به نگهداری خاص اولویت دارد (و الزامات استحکامی بحرانی نیست)، 6013 گزینهی مناسبتر و عملیتری است.
تفاوت در نگهداری و ذخیرهسازی چیست؟
6013 نیاز به نگهداری ویژهای ندارد و میتوان آن را در بستهبندی اصلی و در محیط خشک نگهداری کرد. 7018 به شدت به رطوبت حساس است و باید پس از باز شدن بستهبندی، در آونهای نگهداری (حدود 120-150 درجه سانتیگراد) قرار گیرد و در صورت جذب رطوبت، قبل از استفاده در آونهای خشککاری (250-450 درجه سانتیگراد) خشککاری مجدد شود. این تفاوت در نگهداری بسیار مهم است.
آیا میتوان این دو الکترود را جایگزین یکدیگر کرد؟
در کاربردهای سبک و غیرحساس، میتوان از 6013 به جای 7018 استفاده کرد (با در نظر گرفتن کاهش استحکام). اما هرگز نمیتوان در کاربردهای سازهای سنگین، تحت بار زیاد، فشار، یا حساس به ترک (جایی که 7018 الزامی است) از الکترود 6013 استفاده کرد. جایگزینی 6013 به جای 7018 در این موارد میتواند منجر به شکست اتصال شود. بنابراین، جایگزینی یکطرفه و مشروط امکانپذیر است، اما جایگزینی کامل و دوطرفه خیر.