فروردین 26, 1404
جوشکاری قوسی یکی از مراحل حیاتی در صنایع ساخت و تولید محسوب میشود؛ فرایندی که برای ایجاد اتصالات محکم و ماندگار میان قطعات فلزی نقش کلیدی ایفا میکند. چه در حال جوش دادن یک حصار ساده باشید، چه درگیر ساخت بخشی از یک ماشین پیچیده، کیفیت نهایی جوش اهمیت بالایی دارد. اما رسیدن به جوشی قوی و استاندارد، فقط به مهارت جوشکار محدود نمیشود؛ یکی از مؤثرترین عوامل در این مسیر، انتخاب درست الکترود جوشکاری است.
با وجود اینهمه تنوع در نوع و مدل الکترودها، انتخاب گزینه مناسب ممکن است کمی گیجکننده بهنظر برسد. اما نگران نباشید! در ادامه، مهمترین نکاتی که باید هنگام انتخاب الکترود جوشکاری قوسی مدنظر داشته باشید را با هم بررسی میکنیم تا در هر پروژهای، انتخابی مطمئن و فنی داشته باشید.
شناخت الکترودهای جوشکاری قوسی
پیش از آنکه سراغ بررسی عوامل مؤثر در انتخاب الکترود برویم، لازم است ابتدا با ماهیت الکترودهای جوشکاری قوسی آشنا شویم. الکترود، در واقع میلهای رساناست که در فرایند جوشکاری وظیفهی ایجاد قوس الکتریکی بین دستگاه جوش و فلزات مورد جوشکاری را بر عهده دارد. این قوس الکتریکی، حرارتی بسیار بالا تولید میکند که باعث ذوب شدن فلز پایه و تشکیل یک اتصال محکم و یکنواخت بین قطعات میشود.
اما همهی الکترودها عملکرد یکسانی ندارند. بهطور کلی، الکترودهای مورد استفاده در جوشکاری قوسی به دو دسته اصلی تقسیم میشوند:
● الکترودهای مصرفشدنی (Consumable Electrodes)
این نوع الکترودها در حین جوشکاری ذوب شده و بخشی از فلز جوش را تشکیل میدهند. نمونههای شناختهشده آنها شامل الکترودهای دستی (SMAW) یا همان الکترودهای روکشدار و سیمهای جوشکاری نیمهاتوماتیک (GMAW) هستند که در دستگاههای میگ/مگ به کار میروند. استفاده از این الکترودها در بسیاری از پروژههای ساختمانی و صنعتی بسیار رایج است.
● الکترودهای غیرمصرفی (Non-Consumable Electrodes)
برخلاف نوع قبل، این الکترودها در طول فرایند جوشکاری ذوب نمیشوند. معروفترین نمونهی این گروه، الکترود تنگستن است که در جوشکاری تیگ (GTAW) استفاده میشود. این نوع الکترود، به دلیل کنترلپذیری بالا، در صنایعی مثل خودروسازی یا صنایع دقیق مورد توجه قرار میگیرد.
درک تفاوتها و ویژگیهای هر نوع الکترود، نقش بسیار مهمی در انتخاب درست و موفقیتآمیز آن دارد. انتخاب نادرست میتواند منجر به ضعف جوش، ظاهر نامناسب، یا حتی شکست سازهای شود. به همین دلیل، شناخت ابتدایی این تقسیمبندی به شما کمک میکند تا پایهی تصمیمگیری درستی داشته باشید و جوشی با کیفیت، ایمن و متناسب با نیاز پروژه تحویل دهید.
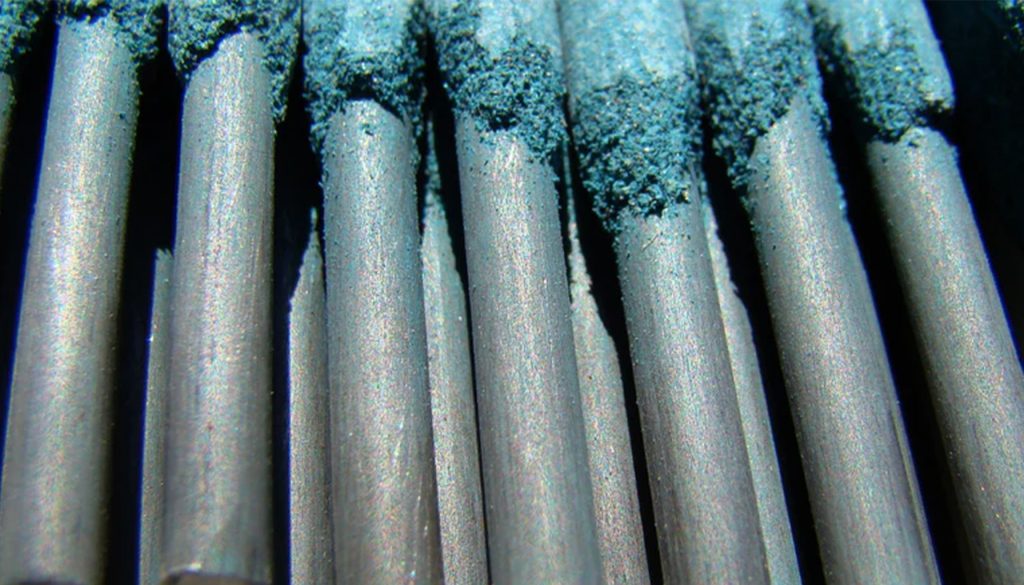
انتخاب الکترودهای جوشکاری قوسی: کلید ایجاد اتصالات بینقص
انتخاب الکترود مناسب، قلب تپنده یک جوشکاری قوسی موفق است. الکترود نه تنها به عنوان ماده پرکننده عمل میکند، بلکه نقش تعیینکنندهای در خواص نهایی جوش، از جمله استحکام، چقرمگی و مقاومت در برابر خوردگی ایفا میکند. انتخاب نادرست الکترود میتواند منجر به جوشهای ضعیف، ترک خوردگی، پاشش زیاد و در نهایت، شکست اتصال گردد. بنابراین، درک عوامل مؤثر در انتخاب الکترود مناسب، برای هر جوشکار حرفهای و مبتدی امری ضروری است. در ادامه، به بررسی دقیق و جذاب این عوامل میپردازیم:
- جنس قطعه کار: همخوانی مواد، ضامن استحکام
نخستین و مهمترین گام در انتخاب الکترود جوشکاری، شناخت دقیق جنس قطعه یا قطعاتی است که قصد اتصال آنها را دارید. تطابق جنس الکترود با فلز پایه، شرط اساسی دستیابی به یک جوش قوی و بادوام است. تصور کنید در حال ساخت یک بنای آجری هستید؛ آیا منطقی است که از خشتهای چوبی برای این کار استفاده کنید؟ مسلماً خیر! در جوشکاری نیز همین اصل صادق است. خواص منحصربهفرد هر فلز، از نقطه ذوب و هدایت حرارتی گرفته تا ترکیب شیمیایی، ایجاب میکند که الکترودی با ترکیبات و ویژگیهای مشابه انتخاب شود.
به عنوان مثال، برای جوشکاری فولاد نرم (Mild Steel)، الکترودهایی نظیر E6010 (با قابلیت نفوذ عمیق و مناسب برای پاسهای ریشه) یا E7018 (با رسوب فلز جوش با کیفیت بالا و خواص مکانیکی عالی) گزینههای مناسبی خواهند بود. در مقابل، برای اتصال فولاد زنگنزن (Stainless Steel)، به الکترودی با آلیاژهای خاص مانند ER308L نیاز است که مقاومت در برابر خوردگی جوش را تضمین کند و از تشکیل کاربیدهای مضر جلوگیری نماید. استفاده از الکترود نامناسب نه تنها استحکام جوش را به خطر میاندازد، بلکه میتواند منجر به ترک خوردگی، ایجاد مناطق ترد و شکننده و کاهش مقاومت در برابر عوامل محیطی شود. بنابراین، همواره قبل از شروع جوشکاری، از انتخاب الکترود سازگار با جنس قطعه کار خود اطمینان حاصل کنید.
- وضعیت جوشکاری: تسلط بر زوایا، کلید کیفیت
وضعیت جوشکاری به جهتگیری اتصال جوش نسبت به جوشکار و زمین اشاره دارد. چهار وضعیت رایج جوشکاری عبارتند از: تخت (Flat)، افقی (Horizontal)، عمودی (Vertical) و بالاسری (Overhead). برخی از الکترودها چندمنظوره بوده و میتوان از آنها در چندین وضعیت استفاده کرد، در حالی که برخی دیگر به طور خاص برای یک یا دو وضعیت طراحی شدهاند. انتخاب الکترود مناسب با وضعیت جوشکاری، تسلط جوشکار را افزایش داده، پاشش مذاب را کاهش میدهد و در نهایت، منجر به جوشهای با کیفیتتری میگردد.
برای نمونه، الکترود E6010 به دلیل سرباره (Slag) سریع انجماد خود، برای جوشکاری در وضعیتهای عمودی و بالاسری بسیار عالی است، زیرا به جوشکار اجازه میدهد تا مذاب را به خوبی کنترل کرده و از ریزش آن جلوگیری کند. در مقابل، الکترود E7018 برای جوشکاری در وضعیتهای تخت و افقی بسیار مناسب است و جوشهای صاف، یکنواخت و با استحکام بالا ایجاد میکند. سرباره این الکترود کندتر منجمد میشود و به مذاب فرصت میدهد تا به خوبی پخش شده و عیوب احتمالی را از بین ببرد. انتخاب الکترود نامناسب برای وضعیت جوشکاری میتواند منجر به مشکلاتی نظیر عدم نفوذ کافی، ایجاد تخلخل و ناخالصی در جوش و کاهش استحکام اتصال گردد.
- ضخامت قطعه کار: تناسب حرارت و نفوذ
ضخامت قطعهای که قصد جوشکاری آن را دارید، به طور قابل توجهی بر انتخاب الکترود تأثیر میگذارد. قطعات ضخیمتر به الکترودهایی نیاز دارند که قابلیت نفوذ عمیقتری داشته باشند و حرارت کافی را برای ذوب و اتصال مناسب فراهم کنند. در مقابل، قطعات نازکتر به الکترودهایی نیاز دارند که کنترل بیشتری را به جوشکار ارائه دهند تا از سوختگی (Burn-through) و ایجاد سوراخ جلوگیری شود.
به عنوان مثال، برای جوشکاری ورقهای نازک فلزی، ممکن است به الکترودی با قطر کوچکتر و جریان آمپر پایین نیاز باشد تا از گرمای بیش از حد و سوراخ شدن ورق جلوگیری شود. در مقابل، برای جوشکاری فولاد ساختمانی ضخیم، به الکترودی با قطر بزرگتر نیاز است که قادر به تحمل جریانهای بالاتر و ایجاد نفوذ کافی در عمق قطعه باشد. انتخاب الکترود با قطر و توانایی نفوذ مناسب با ضخامت قطعه کار، کلید دستیابی به یک اتصال قوی و مطمئن است.
- نوع جریان جوشکاری: سازگاری الکتریکی، تضمین قوس پایدار
نوع جریان جوشکاری مورد استفاده (AC یا DC) نیز در انتخاب الکترود مؤثر است. برخی از الکترودها برای کار با جریان متناوب (AC) طراحی شدهاند، در حالی که برخی دیگر برای جریان مستقیم (DC) مناسبتر هستند.
الکترودهای AC: معمولاً در شرایطی استفاده میشوند که به عملکرد قوس پایدار بر روی موادی مانند آلومینیوم نیاز است. جریان AC میتواند به شکستن لایه اکسید مقاوم روی سطح آلومینیوم کمک کند و قوس پایدارتری را ایجاد نماید.
الکترودهای DC: به دلیل قوس پایدار و یکنواخت خود، برای جوشکاری طیف وسیعی از فلزات از جمله فولاد و فولاد زنگنزن ترجیح داده میشوند. قطبیت جریان DC (مثبت یا منفی بودن الکترود) نیز بر میزان نفوذ و نرخ رسوب فلز جوش تأثیر میگذارد و در انتخاب الکترود باید مد نظر قرار گیرد.
تطبیق الکترود با نوع جریان جوشکاری مناسب، برای دستیابی به کیفیت مطلوب جوش و جلوگیری از مشکلاتی نظیر ناپایداری قوس و پاشش زیاد ضروری است.
- طراحی اتصال و آمادهسازی درز: بستری مناسب برای جوشکاری ایدهآل
طراحی اتصال (مانند لب به لب، روی هم، گوشه و غیره) و کیفیت آمادهسازی درز (Fit-Up) نیز از عوامل حیاتی در انتخاب الکترود به شمار میروند. اتصالات مختلف به ویژگیهای متفاوتی در الکترود نیاز دارند. به عنوان مثال، یک جوش گوشه (Fillet Weld) در یک اتصال روی هم ممکن است به الکترودی با قابلیت پرکنندگی خوب و توانایی ایجاد مقطع جوش مناسب نیاز داشته باشد، مانند الکترود E6010 که نفوذ خوبی نیز ارائه میدهد.
علاوه بر این، اگر آمادهسازی درز به خوبی انجام نشده باشد و فاصلههای زیادی بین قطعات وجود داشته باشد، ممکن است به الکترودی نیاز داشته باشید که بتواند این شکافها را به طور مؤثر پر کند (قابلیت پل زنی خوب). اطمینان از اینکه انتخاب الکترود شما با طراحی اتصال و کیفیت آمادهسازی درز همخوانی دارد، منجر به جوشهای قویتر و مطمئنتری خواهد شد. آمادهسازی صحیح درز، از جمله تمیزکاری و ایجاد فاصله مناسب بین قطعات، به الکترود اجازه میدهد تا به طور مؤثر عمل کرده و یک اتصال یکپارچه و بدون عیب ایجاد کند.
- محیط جوشکاری: تأثیر شرایط بیرونی بر انتخاب درونی
محیطی که در آن جوشکاری انجام میدهید، نقش مهمی در انتخاب الکترود ایفا میکند. جوشکاری در فضای بسته شرایط کنترلشدهتری را فراهم میکند، در حالی که جوشکاری در فضای باز میتواند با چالشهایی نظیر باد، رطوبت و تغییرات دما همراه باشد. انتخاب الکترود مناسب با در نظر گرفتن این شرایط محیطی، تضمینکننده کیفیت جوش یکنواخت و قابل اعتماد خواهد بود.
- جوشکاری در فضای بسته: محیطهای داخلی معمولاً شرایط پایدارتری از نظر دما و رطوبت دارند و از تأثیر مستقیم باد نیز مصون هستند. این امر به جوشکار اجازه میدهد تا از طیف وسیعتری از الکترودها استفاده کند، زیرا نگرانی کمتری در مورد تأثیر عوامل محیطی بر قوس الکتریکی و حوضچه مذاب وجود دارد.
- جوشکاری در فضای باز: جوشکاری در محیطهای بیرونی اغلب نیازمند الکترودهایی است که بتوانند در برابر عوامل محیطی مقاومت کنند. به عنوان مثال، الکترود E6010 به دلیل قابلیت نفوذ عمیق و ویژگی انجماد سریع سرباره، انتخاب مناسبی برای جوشکاری در شرایط وزش باد است، زیرا سرباره سریعاً منجمد شده و از ریزش مذاب جلوگیری میکند. رطوبت نیز میتواند بر عملکرد برخی الکترودها تأثیر منفی بگذارد و منجر به ایجاد تخلخل در جوش شود، بنابراین انتخاب الکترودهایی با پوشش مقاوم در برابر رطوبت در چنین شرایطی حائز اهمیت است. تغییرات دما نیز میتواند بر ویسکوزیته مذاب و رفتار قوس الکتریکی تأثیر بگذارد، که در انتخاب الکترود باید مد نظر قرار گیرد.
- انتخاب الکترود مناسب با محیط جوشکاری، تضمین میکند که کیفیت جوش بدون توجه به شرایط خارجی، ثابت و مطلوب باقی بماند. نادیده گرفتن این عامل میتواند منجر به مشکلاتی نظیر ناپایداری قوس، پاشش زیاد و کاهش کیفیت جوش شود.
- ملاحظات ویژه: فراتر از عوامل اولیه
علاوه بر عوامل اساسی ذکر شده، ملاحظات ویژهای نیز وجود دارند که میتوانند در انتخاب نهایی الکترود تأثیرگذار باشند.
- الزامات کدها و مشخصات فنی: در بسیاری از صنایع، کدهای ساخت و استانداردهای خاصی وجود دارند که نوع الکترودهای مجاز برای استفاده را تعیین میکنند. این کدها به منظور تضمین ایمنی، کیفیت و عملکرد اتصالات جوشکاری تدوین شدهاند. به عنوان مثال، انجمن جوشکاری آمریکا (AWS) سیستم طبقهبندی و مشخصات فنی جامعی برای انواع مختلف الکترودها ارائه میدهد. درک و رعایت این الزامات، به ویژه در صنایعی نظیر ساخت و ساز، کشتیسازی و هوافضا که یکپارچگی جوش از اهمیت بالایی برخوردار است، امری حیاتی است. عدم رعایت این استانداردها میتواند منجر به رد شدن بازرسیها، بروز مشکلات قانونی و حتی خطرات ایمنی شود.
- خواص مکانیکی مورد نظر: خواص مکانیکی مورد انتظار از جوش نهایی، از جمله استحکام کششی، انعطافپذیری (Ductility) و مقاومت در برابر ضربه (Impact Resistance)، باید در انتخاب الکترود مد نظر قرار گیرند. به عنوان مثال، اگر به جوشی با استحکام کششی بالا نیاز دارید، الکترود E7018 انتخاب مناسبی خواهد بود، زیرا رسوب جوش حاصل از آن دارای خواص مکانیکی عالی است. این خواص تضمین میکنند که جوش تحت بارهای مورد انتظار به خوبی عمل کرده و دچار شکستگی یا تغییر شکل ناخواسته نمیشود. انتخاب الکترود با خواص مکانیکی نامناسب میتواند منجر به ضعف ساختاری و کاهش طول عمر مفید قطعه جوشکاری شده گردد.
- هزینه و در دسترس بودن: ایجاد تعادل بین هزینه و عملکرد یک ملاحظه عملی است. در حالی که برخی الکترودهای با کارایی بالا ممکن است نتایج فوقالعادهای ارائه دهند، اما میتوانند گرانقیمت باشند. در مقابل، الکترودهای ارزانتر ممکن است کیفیت مطلوب را ارائه ندهند. یافتن تعادلی که نیازهای پروژه شما را بدون تجاوز از بودجه تأمین کند، مهم است. علاوه بر این، اطمینان حاصل کنید که الکترودهای انتخابی به راحتی در دسترس باشند تا از تأخیر در پروژه جلوگیری شود. گاهی اوقات، انتخاب یک الکترود با عملکرد کمی پایینتر اما با هزینه و دسترسی مناسب، میتواند یک تصمیم منطقی باشد.
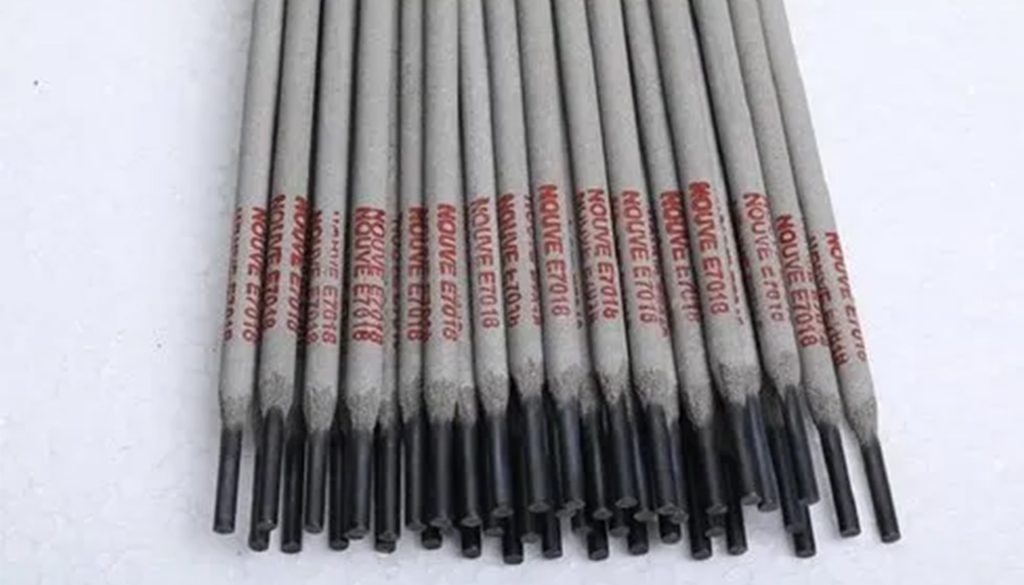
الکترودهای جوشکاری قوسی رایج: آشنایی با پرکاربردترینها
در این بخش، نگاهی به برخی از الکترودهای محبوب و کاربردهای آنها میاندازیم تا با ویژگیهای کلیدی آنها آشنا شوید:
- E6010: به دلیل قابلیت نفوذ عمیق و توانایی کار بر روی سطوح کثیف یا زنگزده شناخته شده است. این الکترود برای جوشکاری خطوط لوله و کارهای تعمیراتی ایدهآل است. قوس قوی و سرباره سریع انجماد آن، کنترل خوبی را در وضعیتهای مختلف جوشکاری فراهم میکند.
- E7018: جوشهای صاف، قوی و با خواص مکانیکی خوب ارائه میدهد. این الکترود معمولاً در جوشکاری فولاد ساختمانی و کاربردهایی که نیاز به استحکام بالا دارند، استفاده میشود. سرباره نرم و آسان جدا شدن آن نیز از مزایای آن به شمار میرود.
- ER308L: یک الکترود فولاد زنگنزن است که برای جوشکاری آلیاژهای مشابه بسیار مناسب است. جوشهای مقاوم در برابر خوردگی ایجاد میکند و در صنایعی که مقاومت به خوردگی اهمیت دارد، کاربرد فراوانی دارد.
- هر الکترود دارای ویژگیهای خاصی است که آن را برای کاربردهای خاص مناسب میسازد. شناخت این ویژگیها به شما کمک میکند تا بهترین انتخاب را برای پروژه خود داشته باشید و به نتایج مطلوب دست یابید.
نکاتی برای انتخاب الکترود مناسب: راهنمایی برای تصمیمگیری آگاهانه
انتخاب الکترود مناسب میتواند چالشبرانگیز باشد، اما این نکات میتوانند به شما کمک کنند:
- نیازهای پروژه خود را درک کنید: جنس، ضخامت و نوع اتصال قطعات را به دقت بررسی کنید.
- وضعیت جوشکاری را در نظر بگیرید: الکترودهایی را انتخاب کنید که با وضعیت جوشکاری شما سازگار باشند.
- شرایط محیطی را مد نظر قرار دهید: الکترودهای مناسب برای استفاده در فضای بسته یا باز را انتخاب کنید.
- به استانداردهای صنعت مراجعه کنید: از انطباق با کدها و مشخصات فنی مربوطه اطمینان حاصل کنید.
- هزینه و عملکرد را متعادل کنید: الکترودی را پیدا کنید که ضمن برآورده کردن نیازهای شما، با بودجهتان نیز همخوانی داشته باشد.
- از اشتباهات رایجی مانند استفاده از الکترودهای ناسازگار یا نادیده گرفتن عوامل محیطی اجتناب کنید. همواره برای بهترین نتیجه، دستورالعملهای سازنده الکترود را مطالعه کنید.
حفظ کیفیت الکترود: نگهداری صحیح، ضامن جوش مرغوب
نگهداری و جابجایی صحیح الکترودها برای حفظ کیفیت آنها ضروری است:
- نگهداری: الکترودها را در مکانی خشک و خنک نگهداری کنید تا از جذب رطوبت جلوگیری شود، زیرا رطوبت میتواند منجر به عیوب جوش گردد.
- جابجایی: الکترودها را با دقت جابجا کنید تا از آسیب دیدن پوشش فلاکس آنها جلوگیری شود. آسیب دیدگی پوشش میتواند بر عملکرد الکترود و کیفیت جوش تأثیر منفی بگذارد.
- بازرسی: به طور منظم الکترودها را از نظر هرگونه علامت آسیب دیدگی یا آلودگی بررسی کنید و برای اطمینان از طول عمر مفید آنها، از روشهای نگهداری توصیه شده پیروی کنید.
با رعایت این نکات، میتوانید از کیفیت الکترودهای خود اطمینان حاصل کرده و جوشهای مرغوب و بادوامی ایجاد کنید.
نتیجهگیری نهایی: انتخاب هوشمندانه، جوشکاری بینقص
انتخاب الکترود جوشکاری قوسی مناسب، فرآیندی چندوجهی است که نیازمند در نظر گرفتن دقیق عوامل گوناگونی از جمله جنس قطعه کار، وضعیت جوشکاری، ضخامت قطعه، نوع جریان، طراحی اتصال و محیط جوشکاری است. با درک این عوامل و پیروی از بهترین شیوهها، میتوانید به جوشهای با کیفیت بالا و بادوام دست یابید که الزامات پروژه شما را به طور کامل برآورده میکنند.
انتخاب هوشمندانه الکترود نه تنها کیفیت جوش را تضمین میکند، بلکه کارایی فرآیند جوشکاری را نیز بهبود میبخشد و از بروز مشکلات و هزینههای ناشی از جوشهای نامناسب جلوگیری میکند. همواره به یاد داشته باشید که مطالعه مشخصات فنی و راهنماییهای سازنده الکترود، گامی اساسی در دستیابی به نتایج مطلوب در جوشکاری قوسی است. با کسب دانش و تجربه کافی در این زمینه، میتوانید به یک جوشکار ماهر و موفق تبدیل شوید.
پرسشهای متداول درباره انتخاب الکترودهای جوشکاری قوسی: پاسخ به ابهامات رایج
در این بخش، به برخی از پرتکرارترین پرسشها پیرامون انتخاب الکترودهای جوشکاری قوسی پاسخ میدهیم تا ابهامات موجود برطرف شده و راهنماییهای عملی برای انتخاب صحیح الکترود ارائه گردد.
بهترین الکترود برای جوشکاری فولاد نرم چیست؟
الکترودهای E6010 و E7018 از جمله پرکاربردترین و بهترین گزینهها برای جوشکاری فولاد نرم به شمار میروند. الکترود E6010 به دلیل قابلیت نفوذ عمیق و توانایی جوشکاری سطوح با کمی آلودگی یا زنگزدگی، برای پاسهای ریشه و جوشکاری در وضعیتهای مختلف بسیار مناسب است. در مقابل، الکترود E7018 جوشهای صاف، قوی و با خواص مکانیکی عالی ایجاد میکند و برای کاربردهای عمومی و سازهای که کیفیت و استحکام بالایی مورد نیاز است، ایدهآل میباشد. انتخاب بین این دو الکترود اغلب به نوع اتصال، ضخامت قطعه و وضعیت جوشکاری بستگی دارد.
آیا میتوان از یک الکترود برای وضعیتهای مختلف جوشکاری استفاده کرد؟
بله، برخی از الکترودها مانند E6010 چندمنظوره بوده و میتوان از آنها در وضعیتهای مختلف جوشکاری (تخت، افقی، عمودی و بالاسری) استفاده کرد. با این حال، مهم است که مشخصات فنی و توصیههای سازنده الکترود را بررسی کنید، زیرا برخی الکترودها به طور خاص برای یک یا چند وضعیت محدود طراحی شدهاند. استفاده از الکترود نامناسب برای یک وضعیت خاص میتواند منجر به مشکلاتی نظیر کنترل ضعیف مذاب، پاشش زیاد و کاهش کیفیت جوش شود.
قطر الکترود چگونه بر فرآیند جوشکاری تأثیر میگذارد؟
قطر الکترود به طور مستقیم بر میزان حرارت ورودی و عمق نفوذ جوش تأثیر میگذارد. الکترودهای ضخیمتر جریان بالاتری را تحمل میکنند و حرارت بیشتری تولید میکنند، که برای نفوذ عمیقتر در مواد ضخیمتر مناسب است. در مقابل، الکترودهای نازکتر با جریان پایینتری کار میکنند و کنترل بهتری را برای جوشکاری مواد نازک فراهم میکنند و از سوختگی جلوگیری میکنند. انتخاب قطر مناسب الکترود با توجه به ضخامت قطعه کار، نقش کلیدی در دستیابی به یک جوش با کیفیت و استحکام مطلوب دارد.
نشانههای استفاده از الکترود نامناسب چیست؟
استفاده از الکترود نامناسب میتواند با علائم مختلفی در ظاهر و کیفیت جوش همراه باشد. برخی از این نشانهها عبارتند از: ظاهر نامناسب جوش (ناهموار، دارای بریدگی کنار جوش)، پاشش بیش از حد مذاب، عدم نفوذ کافی در قطعه کار، و بروز عیوب جوش مانند ترک خوردگی، تخلخل (حفرههای گازی) یا سرباره محبوس شده. مشاهده این علائم هشداری است که نشان میدهد باید در انتخاب الکترود و تنظیمات دستگاه جوش تجدید نظر کنید.
چگونه الکترودهای جوشکاری را برای افزایش طول عمر آنها نگهداری کنم؟
برای اطمینان از حفظ کیفیت و افزایش طول عمر الکترودهای جوشکاری، آنها را در مکانی خشک و خنک نگهداری کنید. بهترین روش، نگهداری الکترودها در بستهبندی اصلی یا یک محفظه در بسته است تا از جذب رطوبت و آلودگی جلوگیری شود. رطوبت جذب شده توسط پوشش الکترود میتواند منجر به مشکلاتی در قوس الکتریکی و کیفیت جوش شود. همچنین، از آسیب رساندن به پوشش فلاکس الکترودها در هنگام جابجایی خودداری کنید.